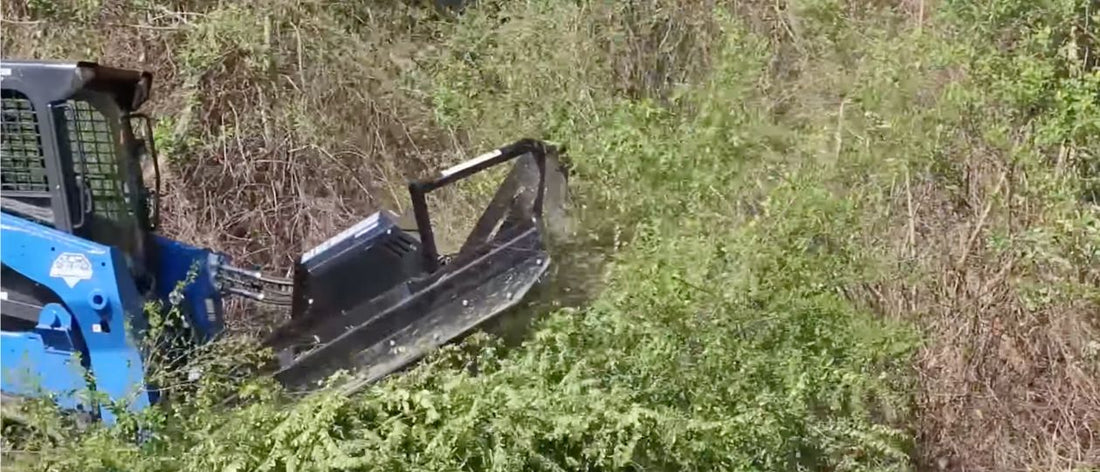
The Best Skid Steer Brush Cutter | Know What To Look For
Share
A skid steer brush cutter is a great tool to have on your farm, ranch or landscaping business. They are perfect for clearing away brush, undergrowth and breaking new farm land.
Not all brush cutters are built equally, so it can be tough to know which one is the best for your needs. In this blog post, we will have a look at open vs close front designs, types of hydraulic motors used and types of blade carriers used in the hopes of helping you choose the best skid steer brush cutter for your needs.
The Basics | What is a Skid Steer Brush Cutter?
Skid steer brush cutters go by several different names, some customers refer to them as mowers, brush hogs, and and some times just simply cutters. No matter what you want to call them, they are all the same thing.
A skid steer brush cutter is an attachment that connects to the front of your skid steer loader using a universal quick attach system. You use the attached hydraulic hoses and couplers to attach to your skid steer's auxiliary hydraulic system, which powers a hydraulic motor connected to a spindle. The spindle connects to a blade carrier, which hold several cutting blades. These blades swing outwards with centrifugal force to cut down grass and bush.
Many manufacturers have reengineered this system to make them more powerful and efficient, therefore, not every brush cutter is built equally. Some are better suited for thick brush, while others are better suited to give you a nice finish on overgrown grass.
So the first step in determining what brush cutter is the best for you, you should consider some of the main design features.
Open Front Vs. Closed Front Brush Skid Steer Brush Cutters | Which is Best?
One of the first things you'll notice when comparing brush cutters is that some of them are open in the front, while others are squared off with a closed front. This is where we will start our discussion on choosing the right skid steer brush cutter for your needs.
Closed Front Brush Cutters
A closed front brush cutter has a rectangular design and is closed off on all four sides. The left and the right side of the cutter will be closed off with welded steel, while the front will often have a chain curtain. The chain curtain allows material to flow into the cutter while the skid steer moves forward, but helps prevent material from flying out while it's being cut.
The back will normally have a taper to it to allow material to flow out of the brush cutter as the skid steer moves forward. Alternatively, some models may use a chain curtain at the back of the brush cutter to allow material to flow out while the skid steer moves forward.
When is a Closed Front Brush Cutter The best Choice?
Having the blade carrier and blades closed in on all four sides keeps the cut material inside of the brush cutter attachment for longer amount of time.
Keeping material inside the brush cutter for longer results in a "nicer" finish with smaller and more manageable amounts of debris left over after the cut. This makes it a common choice for customers who are looking to cut over grown parkland and pasture where a nice finish is desirable.
What's the Drawback?
The drawback to having a closed front brush cutter is that it can be more difficult to get thick woody material into the cutter. This makes it a bit more challenging to use in dense brush where the front of the cutter may prevent material from easily getting into the cutter.
This isn't to say that you can't angle deck of the cutter upwards with your loader arms to expose the blades to more of the brush, however, this still doesn't match the efficiency of an open front brush cutter when attacking thick bush.
So, all of that to say, closed front brush cutters should be one of your first considerations when you are going to be brush cutting in thick grasses and would benefit from a nice finish.
Open Front Skid Steer Brush Cutters
An open front skid steer brush cutter will be closed off with welded steel on both left and right side of the cutter. The front of the cutter will be cut out, usually with two 45 degree angles to expose the cutting blades. The back of the cutter will have a chain curtain to allow material to exit easily while the cutter is moving forward.
When is an Open Front Brush Cutter The Best Choice?
Open front brush cutter attachments are more aggressive than their closed front counterparts making them perfect for dense brush. Having an open front allows the cutting teeth to aggressively reach out in front of the deck of the cutter and start attacking brush before it gets underneath the cutter.
What's the Drawback?
There has to be a draw back to all that aggressive cutting right? Yes, of course there is.. Because material is being cut before it gets under the deck, as well as the cutter having less deck area all together, cut material is being hacked and thrown out much more aggressively than with the closed front. This leaves you with more flying debris and larger pieces of debris left over when you are done cutting.
From our experience, open front brush cutters are far more popular than closed fronts. Many customers prefer to have the ability to aggressively attack thick brush.
Hydraulic Motors | What Do I Need To Know?
Sizing the right motor to your skid steer's hydraulic system is an important consideration when your are picking a new brush cutter. There is some misconception that you need a high flow skid steer to run a brush cutter attachment, and this simply isn't true.
Although high flow may get your brush cutter spinning up to speed slightly quicker, once you are up and running, a standard flow skid steer brush cutter will do everything a high hydraulic flow cutter will do.
Manufacturers will design and build each model of brush cutter to be used with a specific range of hydraulic flow. You should ensure your skid steer will operate within this range in order to get the best performance and longevity out of your brush cutter. It should also be noted that operating outside of this hydraulic flow range will likely void your warranty.
What Type Of Hydraulic Motors Are Used In Brush Cutters?
Most skid steer brush cutters will come with a "direct drive" hydraulic motor. This means that the motor will directly drive the spindle and blade carrier, without reduction gears, chains or belts involved.
Because there are several common types of hydraulic motors available on the market (gear, vane and piston), knowing which one your brush cutter uses is an important consideration. Each type of motor has distinct advantages and sometimes the type of motor used is all that stands between a brush cutter being branded as "Heavy Duty" or "Severe Duty".
The gear/vane type of hydraulic motors are typically used in lower cost and lower power applications, while piston type motors are used in higher cost and high power applications.
Gear & Vane Hydraulic Motors
Hydraulic motors that use gears or vanes to transfer hydraulic flow into rotational torque are used in countless attachments. Although the two style motors are fundamentally different in how the operate, they share several similar characteristics:
- They are typically around 70% efficient. Out of 100% of the hydraulic flow and pressure that your skid steer is able to push into the motor, only 70% of it is going to be used to create rotational torque.
- They provide high speed rotation at low torque. This is referred to as a High Speed, Low Torque (HSLT) motor. At first thought this may not seem like a bad thing, however, brush cutters operate better with the exact opposite - lower speed and higher torque.
- They don't operate smoothly at low hydraulic flow rates. Although this may not be everyone's biggest concern, it may be an important consideration for low flow skid steers.
- They are cheap to manufacture. It's all relative, however, when compared to piston style motors, gear and vane style motors are cheap to manufacturer and find their way onto many attachments for this reason alone.
But it's not all bad! So what are the advantages?
- They will "better tolerate" lousy maintenance. To be clear, nothing will tolerate lousy maintenance. But when compared to a piston motor, gear and vane motors will most likely be able to stomach a bit more abuse.
- They are less prone to catastrophic failure. From our experience, gear and vane style motors will wear out slowly before failure rather than suddenly experiencing large failures.
Hydraulic Piston Motors
A radial piston motor solves many of the problems of the vane and gear style motor with only a few trade offs.
- A Radial Piston motor is up to 97% efficient. Being able to capture more power from your skid steers auxiliary hydraulic system gives your brush cutter more power. The extra power allows you to attack thick brush at higher speeds.
- A Radial Piston Motor Operates at Lower Speeds with Higher Torque. The higher torque keeps your cutting blades cutting with less tendency to slow down when pushing into thick brush.
- A Radial Piston Motor Operates Smoothly at Low Flow Rates. This makes them a good choice for low flow skid steers.

The trade off for all this extra torque and power is (as you've guessed by now), radial piston motors are expensive and won't tolerate poor maintenance such as hydraulic fluid contamination.
Hydraulic Pressure Gauges
This is a good place to mention that many high quality skid steer brush cutters will come with a hydraulic pressure gauge built into them. These gauges are on the top of the brush cutter facing backwards so that the skid steer operator can easily see it.
These pressure gauges are a great feature on brush cutters, but we often come across customers confused about how they work. It's not uncommon for us to get calls from customers telling us that they have the brush cutter hooked up, revved up, and they can't can't any pressure to build on the gauge.
This is normal - the gauge indicates hydraulic back pressure, and therefore pressure won't build until you start pushing into brush. But why do we care about hydraulic back pressure? Because it is the best measure of how hard you can push your brush cutter. Pressure gauges are colour coded so that you can keep the pressure in the green area and out of the red.

If the brush cutter starts to build pressure into the red "high pressure" area while you are attacking brush, you know that there is too much back pressure and you need to back off and slow the skid steers travel speed down for the brush cutter to be running at optimal efficiency. Likewise, if the gauge is showing that you are cutting below the green pressure arc, you know you can pick up your speed and cut harder and faster.
This isn't a standard feature on all skid steer brush cutters, so it should be considered when you are comparing features.
So what Motor Is Best For Skid Steer Brush Cutters?
To put it simply, a radial piston motor is the best choice for skid steer brush cutters. You'll notice piston motors are often used in skid steer brush cutters that are branded as "Severe Duty" or "Heavy Duty." The piston motor is usually a large part of why the cutter has been labeled and marketed this way. Often these brush cutters will have thicker decks and larger blade carriers to accompany the more powerful motor.
Standard duty skid steer brush cutters are likely to be fitted with gear or vane type of hydraulic motors to keep them affordable. On a quality brush cutter, this may be just fine for lighter use in thick grass.
All that to say, when you are comparing skid steer brush cutters trying to find the best, I would suggest choosing one with a piston motor and committing yourself to the higher purchase price and maintenance schedule.
Blades and Blade Carriers | What To Think About?
Now that we have the perfect hydraulic motor to apply rotational torque, it's time to think about what all that torque is rotating! This is where the blade carrier and blades come in.
Blade carriers take on a few different shapes, weights, and can carry different number of blades. We should also consider how easy or difficult it is to change blades, as well as if the blade carrier has any additional features to help prevent entanglements and damage with debris.
Blade Carriers | The Different Shapes
Maybe the first and most obvious thing you'll notice about blade carriers is that they come in two different shapes, triangular and circular. Triangular blade carriers are used with brush cutters that have a three blade cutting system, while circular blade carriers are used with a 4 blade cutting system.
Manufacturers have to pay special attention to ensuring blade carriers are balanced during the manufacturing process. Some blade carriers weigh over 500 pounds so any unequal distribution of weight will easily vibrate straight through the attachment and skid steer.
Triangular 3 Blade Carrier
A triangular blade carrier has less surface area than a circular one and is therefore lighter. And this is the main point about triangular 3 blade carriers, it's lighter and therefore better suited for lower torque brush cutters.
A low power hydraulic motor will have an easier time trying to keep a light blade carrier turning at cutting speed when met with resistance. It's important to understand that the lighter weight makes the hydraulic motors job easier, but this doesn't translate into more torque or cutting power.
A three blade triangular cutting system is also doing less cutting than a four blade system per rotation of the blade carrier. Once again though, this makes it easier for a weaker hydraulic motor to keep up, because less cutting per rotation means less resistance.
Overall a triangular 3 blade carrier is best suited for light duty work, on a brush cutter with a vane or gear type hydraulic motor. This system will perform best in grass and very light bush.
Circular 4 Blade Carrier
Brush cutter attachments with a circular blade carrier will hold 4 blades, have more surface area and be heavier than a triangular blade carrier. The extra blade performs more cutting per rotation, and the heavier blade carrier has more inertia to keep it cutting when met with resistance.
Circular blade carriers are often up to 1/2" thick, weigh over 500 pounds, and need a massive amount of reliable torque to operate. This is why you should ensure it is paired with a radial piston motor or similar.
Some manufacturers have added a serrated edge to their circular blade carriers. This blade carrier paired with a piston motor and open front design brush cutter is extremely aggressive, and can be used to attack the thickest bush.
Cutting Blades
A quality brush cutter will be designed with "drop down" blades that are bolted onto the blade carrier. The drop down blades get the blades closer to the surface for a closer cut, but will also help to prevent damage if you happen to pick up fence wire or other entangling debris.
The blades on a brush cutter attachment take a lot of abuse, and should be made of high quality steel and be easy to replace and maintain. That's why we always suggest looking for a skid steer brush cutter that allows for access to the blades through the top of the deck.
For example, on some open front brush cutters, you can open a maintenance panel on the front of the brush cutter to gain access to the bolts holding the blades to the carrier. The makes blade replacement an easier task.
Putting It All Together | Ready To Choose The Best Skid Steer Brush Cutter?
To summarize, skid steer brush cutter attachments are either built to be big and powerful or light and less expensive. With your new found knowledge of motors, deck designs and blade carriers, you'll have an easier time spotting which one is which!
To be clear, there is a strong market for the lighter and more affordable brush cutters, so long as you know it's limitations, and don't expect it to be able to rip up dense brush. You also may not benefit from a severe duty brush cutter if all you are planning on doing is cutting the over grown grass around the yard.
So next time your are in the market for a new skid steer brush cutter, be sure to have a look at the specifics, and reach out to our team if you need to know more.
Ready to check out our collection of skid steer brush cutters? Click Here!